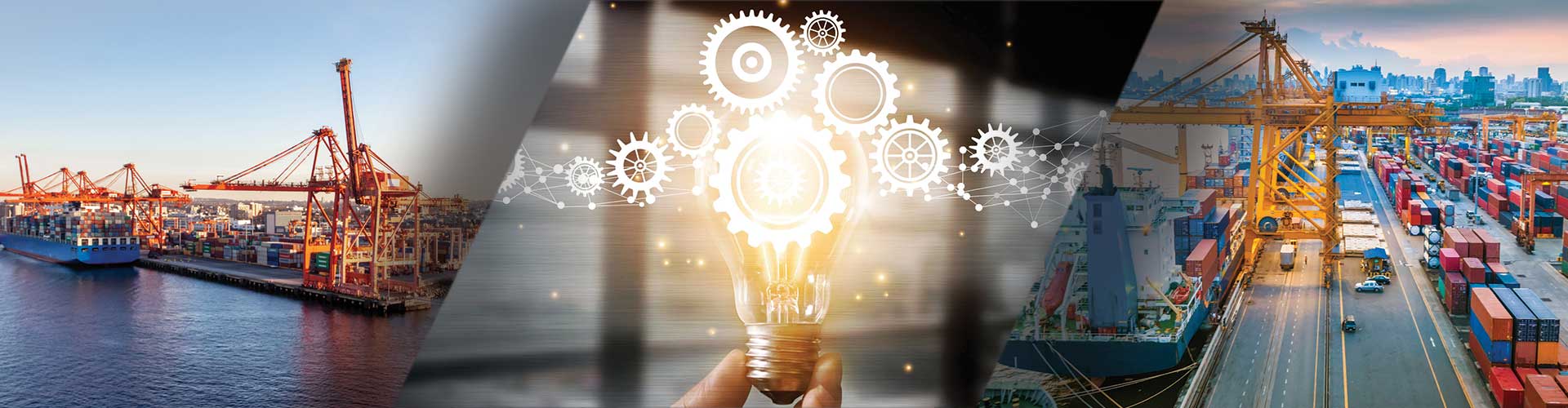
Port Automation Case Study
Situation: A port facility for receiving, storing, and shipping grain. It was designed and constructed between 2018 and 2020, ramping up to full operation in 2021. The terminal required not just a process control system, but a system to keep a complete audit trail of all transactions and meet all legal requirements for shipping grain. They relied on Comco’s technical and industry expertise to design, implement and support the system.
Comco Solution
Comco provided a complete turnkey Electrical & Control solution in partnership with CEL Electrical Contractors. The Comco solution comprised of the following:
Control System Hardware
Comco designed and supplied all control system computers and panels, including PLC, remote I/O and motor starters. System highlights included:
Engineering Services
Comco provided electrical, control and instrumentation design services for the whole facility. All engineering drawings went through a design review process and were sealed by a professional engineer upon issue for construction. An ‘as-built’ drawing set was also created to incorporate construction and commissioning changes and allow management to accurately maintain the facility.
Commissioning and Operational Support
Experienced Comco technicians performed on-site and/or remote commissioning and operator training. Commissioning included specialized services like smart device configuration and programming of managed network switches. Comco continues to provide 24/7 operational support.
Control System Software
Comco developed fit-for-purpose, custom PLC programming and Human-Machine-Interface (HMI) graphics and functionality to meet the unique requirements of the facility. Main functionality of the system included:
- Transactions for receiving, storing, transferring, cleaning, blending and shipping multiple different commodities.
- Receiving from rail and shipping via vessel, container or truck.
- Controlling multiple automatic transactions simultaneously while preventing cross contamination.
- Optimized bulk weigher control with accurate gate control via VFD and dynamic free fall calculation.
- Complete audit trail of all transactions, weighments, and user actions.
- Bulk weigher virtual ticket printing solution meeting Canadian Grain Commission (CGC) requirements.
- Video and screen recordings to meet CGC requirements for an Automated Weight Recording and Playback System (AWRAPS).
- Manual and maintenance control modes to provide flexibility and error recovery.
- Operational data storage for preventive maintenance purposes.
- Integration with multiple third party systems, e.g. ship loader, container tipper, rail indexer, RFID rail car scanners, and truck and bulk weigher scale heads.
- Integration between control and business networks, including multiple CCTV cameras, smart video intercom and gate control systems.
- Custom reporting for daily operations, vessel loadout, rail car to destination inventory tracking, and site event recording.
- Monitoring and alarm reporting of smart devices like UPSs.
- Multi-user and multi-role HMI logins.
Control System Software Value-add
Apart from an innovative design and fit-for-purpose functionality, Comco’s approach provided much added value:
- Our turnkey solution provided a one stop shop for the customer for all electrical and control aspects of the project.
- With Comco and CEL taking responsibility for designing and building the facility as an integrated team, it significantly reduced the cost and effort required by the customer to manage multiple vendors and contractors.
- Our experienced team made sure that the electrical design and control system functionality met all code and legal requirements, while also incorporating customer preferences.
- While facilitating accurate steady state control of simultaneous processes, the added value of the Comco system really comes to the fore when handling upset conditions, allowing flexibility in operations while still maintaining safe operating boundaries, and performing disaster recovery.
- Operational support any time of the day or night is provided by a knowledgeable team, typically members who worked on the original project.

We believe in building long-term, trusting relationships and work hard every day to be the best automation company in the world for every size and budget with 24/7 support. Contact us today, and let us show you how Comco can benefit your business.