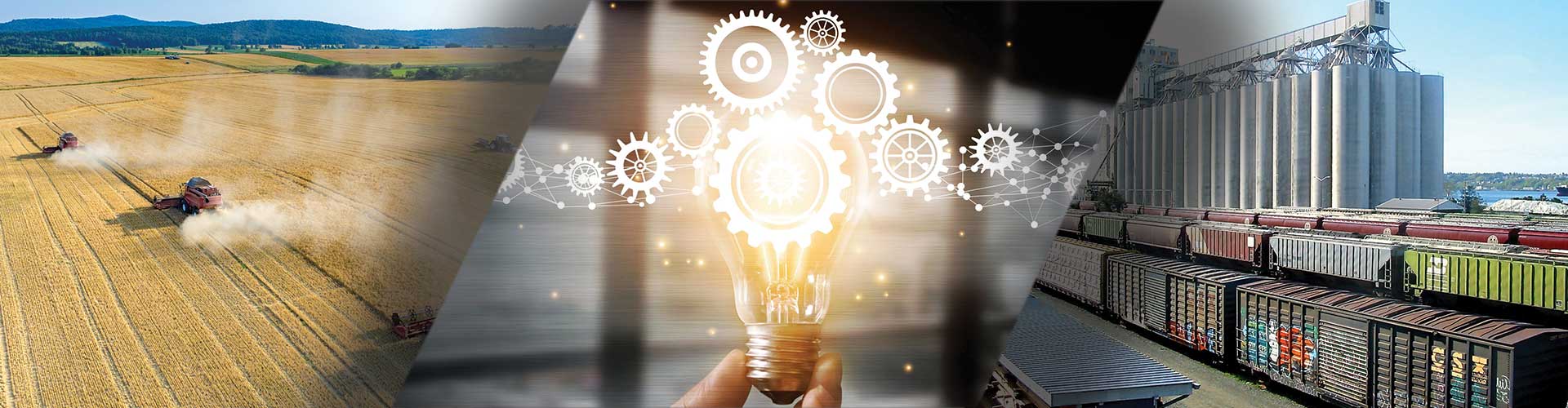
Grain Terminal Automation Case Study: Aurora Cooperatives
Situation: Aurora Cooperative has multiple grain elevator facilities in United States- Superior NE, Aurora NE, Grand Island NE & Sedan NE. While some sites had existing automation system, one of the sites was greenfield. Aurora wanted to work with a partner that could provide easy to use system customized to each site, available 24×7 to provide support and work with their existing electrical contractors.
Comco Solution
Comco provided complete turnkey control system solution from electrical/control design services to implementation to post-commissioning support.
Comco Solution
Control System –Comco developed custom PLC control systems with custom HMI graphics at each site to maximize operations. The HMI at all sites had same look and feel but customized to individual flow diagram. The HMIs designated separate transactions (ie receiving, shipping etc.) by color for easy visual differentiation. Finally, the system audit log tracked every mouse click, security log-in change or user entry action. .
Engineering Services – Comco provided electrical design services such that all drawings were clear and accurate for electricians to follow on site. It also included the design for all new PLC panels.
PLC Panels: All PLC Panels were CSA / CSAUS certified, designed with the best components and tested comprehensively prior to shipping including communication with any existing site panels
Alarms and notification: Comco created an alarming module that notified senior managers and senior safety managers at Aurora Coop, via their pre-entered cell numbers, of critical alarms as they are activated within any of the Comco control systems at any of the Aurora Coop sites. Alarms were clearly identified with the alarm device turning bright red with a date & time stamp and a text description
Commissioning – Comco provided on-site training (System Usage and PLC troubleshooting) and commissioning services for all of the Aurora sites. All the panels / IO were fully tested to the end devices and that all routes and interlocks were tested for the appropriate control system reaction alongside the electricians and operations team.
Comco Value-add
- Comco system allows managers to train full-time and seasonal employees easily, run the control systems at any of the sites and move employees around from site to site (as required) during the busy seasons.
- The system enabled senior managers to be in the loop with all critical alarms that are being generated so that they can take the appropriate actions necessary to address the situation in a timely manner.
- The system provided comprehensive picture of facility’s day to day operations including alarm history to identify issues in the field and understand what is required to resolve the problem.
- Comco’s 24×7 support has ensured all issues are resolved in a timely fashion to reduce down-time including site visits as required and replacement of hardware parts/PLC panels.
Nate Panko
Northern Area Grain Manager - Aurora Cooperatives

We believe in building long-term, trusting relationships and work hard every day to be the best automation company in the world for every size and budget with 24/7 support. Contact us today, and let us show you how Comco can benefit your business.
Fit-For-Purpose Automation Solutions
PLC Automation, Process Control, and Engineering Solutions For Your Industry
Case Studies
iIf you’re looking for specifics, the case studies will give you an in-depth look at some of the work we’ve completed for our clients. These success stories highlight how Comco can create custom solutions that work with your existing technology stack for any industry.